Transformation with Technology: Innovative Solution for Steam Lines in a Textile Factory
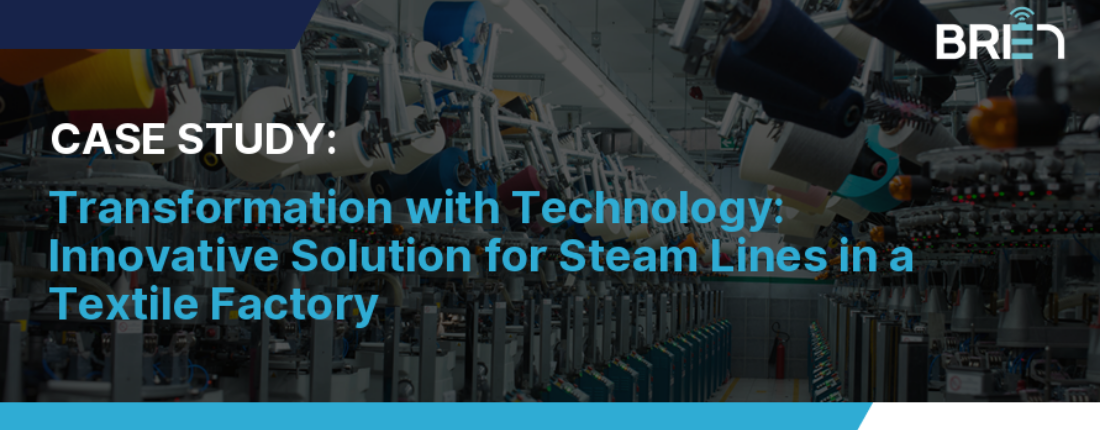
Challenge
A textile mill was struggling with difficulties in manual inspections of steam lines and leakage problems due to old lines. Manual inspections were difficult at high elevations and in inaccessible areas due to the process, while invisible leaks were not being detected, causing serious problems. In addition, steam had to be kept at high pressure so that the machines could operate at maximum efficiency and effectiveness. The factory was focused on reducing energy costs and emissions, and wanted to find a solution to solve the challenges of manual inspections and leakage issues, improve energy efficiency and reduce emissions.
Solution
The textile factory decided to cooperate with Brenpower as a result of the research it conducted to find solutions to the problems it faced. The factory decided to install 100 monitors as a pilot project. These monitors were placed in the dye jets next to the steam traps. When the artificial intelligence learning process was completed, it was able to detect system failures and leaks and send sms and e-mail notifications to the relevant people. In this way, $21,650 was saved with 100 monitors.
Benefits
• Machine learning on a float-type steam trap detected a leak and estimated annual losses of $5,700.
• As the pilot project was successful, the factory decided to expand the deployment across the plant and began the process of scaling up to include all steam traps.
• In order to avoid any production interruptions in the future, preventive maintenance is aimed to be implemented by continuously monitoring the system.
• The resulting energy savings will be used to contribute to efforts to reduce the carbon footprint.